
Recent advancements in robotics have enabled machines to delicately handle fragile objects such as eggs an achievement made possible by fingertip-integrated pressure sensors that provide tactile feedback. However, even the world’s most advanced robots have struggled to accurately detect pressure in environments affected by complex external interference factors such as water, bending, or electromagnetic interference. Our research team has successfully developed a pressure sensor that operates stably without external interference even on a wet smartphone screen and achieves pressure sensing close to the level of human tactile perception.
EE Professor Jun-Bo Yoon’s research team has developed a pressure sensor capable of high-resolution pressure detection even when a smartphone screen is wet from rain or after a shower. Importantly, the sensor is immune to external interference such as “ghost touch” (erroneous touch registration) and maintains its performance under these adverse conditions.
Conventional touch systems typically employ a capacitive pressure sensor because of its simple structure and excellent durability, which makes it widely used in smartphones, wearable devices, and robotic human–machine interfaces. However, these sensors are critically vulnerable to external interference, such as water droplets, electromagnetic interference, or bending-induced deformation that can cause malfunctions.
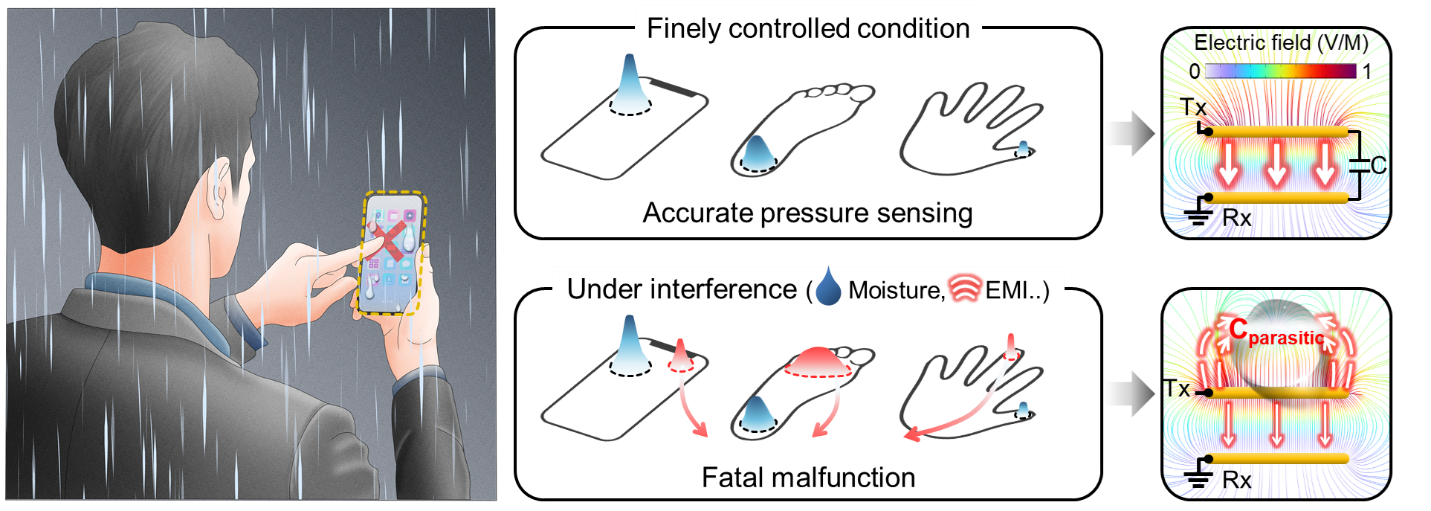
To address this problem, the research team first investigated the root cause of interference in capacitive pressure sensors. They discovered that the “fringe field” generated at the sensor’s edge is extremely vulnerable to external interference.
To fundamentally resolve this issue, the team concluded that suppressing the fringe field—the source of the problem—was essential. Through theoretical analysis, they closely examined the structural variables that affect the fringe field and confirmed that narrowing the electrode gap to the order of several hundred nanometers could suppress the fringe field to below a few percent of its original level.
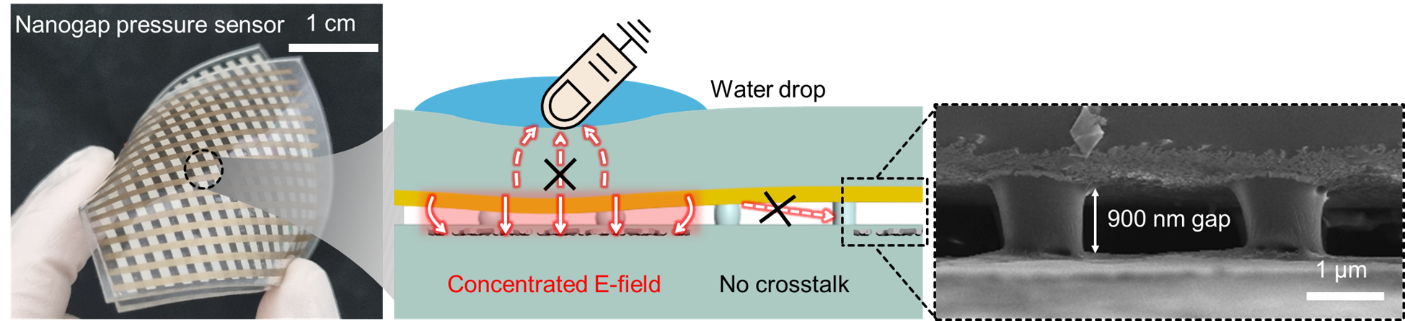
Utilizing proprietary micro/nano fabrication techniques, the research team developed a nanogap pressure sensor with an electrode gap of approximately 900 nanometers. The sensor reliably detected pressure regardless of the applied material and maintained its sensing performance even under bending or electromagnetic interference.
Moreover, by leveraging the characteristics of the developed sensor, the team implemented an artificial tactile system. Human skin employs pressure receptors known as Merkel’s discs for tactile sensing. To mimic this function, a pressure sensor technology that responds solely to pressure while remaining unresponsive to external interference was required, a condition that had proven challenging with previous technologies.
The sensor developed by Professor Yoon’s team overcomes these limitations. Its density reaches a level comparable to that of Merkel’s discs, enabling the realization of a wireless, high-precision artificial tactile system.
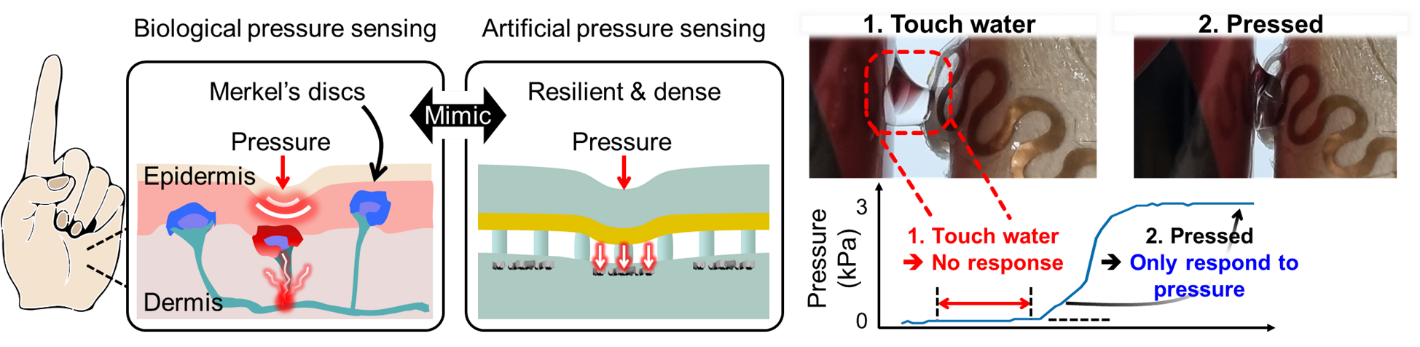
To further explore its applicability in various electronic devices, the team also developed a force touch pad system. They demonstrated that this system could obtain high-resolution measurements of pressure magnitude and distribution without interference.
Professor Yoon commented, “Our nanogap pressure sensor operates reliably without malfunctioning, even on rainy days or in sweaty conditions, unlike conventional pressure sensors. We expect this development to alleviate a common inconvenience experienced in everyday life.”

This research, led by Dr. Jae-Soon Yang, PhD Candidate Myung-Kun Chung, along with contributions from Professor Jae-Young Yoo from Sungkyunkwan University, was published in the renowned international journal Nature Communications on February 27, 2025. (Paper title: “Interference-Free Nanogap Pressure Sensor Array with High Spatial Resolution for Wireless Human-Machine Interfaces Applications”, https://doi.org/10.1038/s41467-025-57232-8)
The study was supported by the National Research Foundation of Korea’s Mid-Career Researcher Support Program and Leading Research Center Support Program.